News Story
Hu Develops Eco-Friendly Process for Natural Bamboo Composite
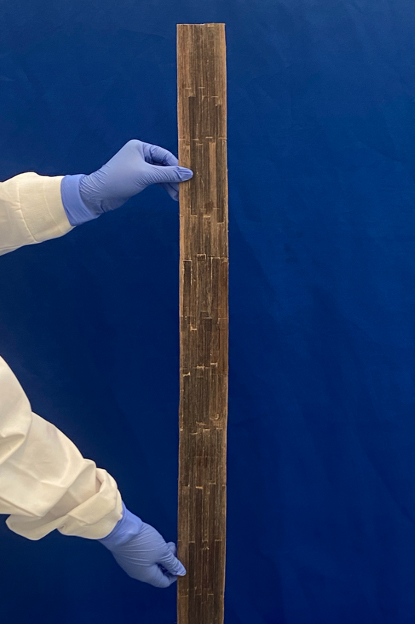
Sample in-situ glued-bamboo (glubam) composite.
Researchers at the Department of Materials Science and Engineering (MSE) developed a new cost-effective bio-adhesion strategy that can process natural bamboo to composites without the use of petroleum-derived synthetic adhesives, speeding up the process for a larger-scale composite operation that can be used in structural engineering applications.
Bamboo composite is an attractive candidate for structural applications in the construction, logistics and automotive industries, but the use of petroleum-derived synthetic adhesives or low-bonding bio-based adhesives has slowed down its widespread usage.
That's why University of Maryland Distinguished Professor Dr. Liangbing Hu developed a novel bio-adhesion technique based on in-situ lignin bonding, which has the capacity to process natural bamboo into a scalable, high-performance composite named “in-situ glued bamboo” (glubam).
"This is the first demonstration that in-situ generated lignin has the right chemistry and morphological arrangement to bond the bamboo pieces together toward a structural material. This concept can then be extended to wood," said Dr. Hu.
Compared with petrochemical-based adhesives, the in-situ lignin adhesion strategy is cost-effective, eco-friendly and has no harmful emissions. This work demonstrates a practical approach for making sustainable large-scale bamboo composites for structural engineering applications that could provide a significant decarbonization impact and promote sustainable forestry practices.
This new development was a collaboration between Dr. Hu and University of Wisconsin-Madison Professor Xuejun Pan.
In this technique, lignin connects the cellulose fibrils into a network via a strong adhesive interface formed by hydrogen bonding and nanoscale entanglement, which results in the processing of in situ glubam, presenting shear strength of 4.4 Megapascals (MPa), and a tensile strength of 300 MPa.
Additional information can be found in Nano Letters, 2023, DOI: https://pubs.acs.org/doi/10.1021/acs.nanolett.3c01497
Published September 12, 2023